GRAPHITE & GRAPHENE THERMAL STRAPS
X-SERIES® | THE WORLD'S HIGHEST PERFORMANCE THERMAL LINKS
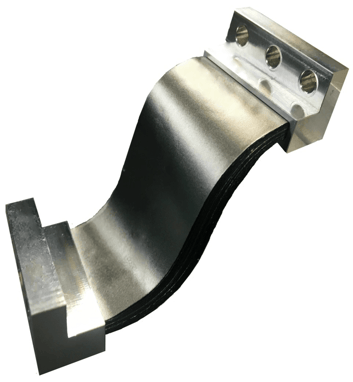
Vibration transmission and waste heat removal requirements have dramatically changed as spacecraft, cubesats, larger satellites, and other aerospace equipment needs have evolved in recent years. Unfortunately, in certain applications, these requirements have effectively eliminated traditional metallic cable, foil, and graphite fiber straps as a solution. To meet these more challenging requirements, TAI offers our X-Series® PyroFlex™ product line; the world's highest thermal performance, "Zero-Stiffness" thermal straps.
- 3 – 4X the performance of equivalent copper and graphite fiber straps
- 10 – 30% greater thermal performance than competing carbon straps
- PyroFlex™ offers 6X the thermal performance of al & 4X the performance of cu at room temp
- PyroFlex™ and Graphene are both 28% lighter than aluminum, and 77% lighter than copper
- PyroFlex™ links are the industry’s most flexible thermal straps
- PyroFlex™ straps are exceptionally clean and passed strict PCL/PAC/FPAC testing
- PyroFlex™ DO NOT REQUIRE ENCAPSULATION SLEEVES
- X-Series® PyroFlex™ straps achieved NASA Technology Readiness Level (TRL) 9 and have Flight Heritage
VISIT THE X-SERIES® THERMAL STRAP DESIGN GALLERY
CUSTOM & STANDARD MODEL X-SERIES® STRAPS
ORDERING YOUR STRAPS
If you have already selected your standard X-Series® model(s) from the catalog, please download and complete the Thermal Strap Design and Ordering Form, and submit the questionnaire to our Director of Business Development at tlink@techapps.com, to receive your quote.
X-SERIES® STRAPS
|
CUSTOM PyroFlex™ STRAPS
Pictured: Custom PGL™ with dual flat aluminum fittings. |
THE INDUSTRY'S HIGHEST THERMAL PERFORMANCE
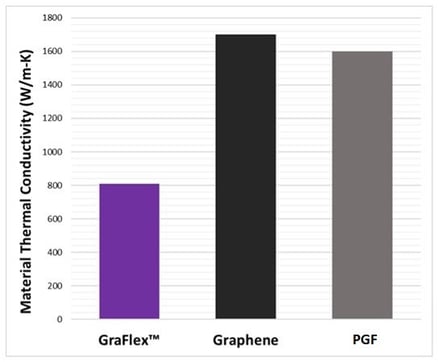
Specific Thermal Conductivity of Strap Materials
|
Thermal Conductivity of Strap Materials
|
SPACE FLIGHT QUALIFICATION
- Thermal Conductance
- Thermal Cycling
- Post-Thermal Cycling Thermal Conductance
- Stiffness
- Vibration
- Post-Vibration Thermal Conductance
- Particulation Contamination Level (PCL)
- Outgassing
- Post-Vibration PCL
Pictured: X6-501 NASA Stiffness Test (October 2018). |
Pictured: Dual X6-501 NASA Vibration Test (November 2018). |
PYROFLEX™ SPACE FLIGHT HERITAGE
- NASA Goddard - PROGRAM NAME WITHHELD AT CUSTOMER REQUEST - straps used for waste heat removal of reaction wheel isolation system (RWIS). Expected launch date: 2028.
- General Atomics - PROGRAM NAME WITHHELD AT CUSTOMER REQUEST - straps used to cool Fast-Steering Mirrors. Expected launch date: 2026.
- Lockheed Martin - MULTIPLE PROGRAM NAMES WITHHELD (DX-RATED) - several designs with both aluminum and high conductivity carbon fittings for multiple military satellite programs. Launch Dates: 2024 - 2028.
- DLR and Aribus DS - MERLIN Program - Straps used to cool optical instruments. Expected launch date: 2028
- University of Hawaii Space Flight Laboratory / NASA JPL - Hyperspectral Thermal Imager (HyTI). Straps used to cool instruments on CubeSat. Launched March 21, 2024.
- Lockheed Martin - ARTEMIS II & III MISSION (ORION) - Dozens of straps used to cool DAQ systems. Expected Launch dates 2025 and 2026.
- Blue Origin - NEW GLENN - Several dozen straps used to cool multiple tanks and other equipment on NG. Expected Launch Date: End of 2024.
- John's Hopkins Applied Physics Lab - IMAP - 10 straps used to cool an avionics box and the IMAP-LO instrument. Expected Launch Date: February 2025.
- Planet Labs - PELICAN CONSTELLATION SATELLITES - dozens of straps used to cool reaction wheels on the satellites. Launch Dates: COMING SOON.
- Numerous CubeSat, NanoSat, military satellites, and Commercial Crew and Cargo Vehicle Customers that are CONFIDENTIAL due to NDA's. Launch Dates: 2022 - 2028.
- Turion Space - DROID 002 MISSION - multiple flight model straps used on satellite program to clean up orbital debris. Launch date - February 2025.
CRYOGENIC APPLICATIONS
Several of TAI's customers have tested our graphite sheet and fiber thermal straps for use in cryogenic applications, ranging from cryocoolers, to medical equipment, and quantum computers, and TAI will be releasing cryogenic performance data in late 2023 / early 2024. Studies have shown that both graphite strap types can be used in place of thermal switches, as they can speed up cool-down times in cryostats and other cold laboratory equipment, but effectively stop transferring heat between 10K and 40K.
PYROFLEX™ - THE "ZERO-STIFFNESS THERMAL STRAP"
HIGH CONDUCTIVITY CARBON FIBER (HCCF) FITTINGS
![]() Pictured: 3 Flight Model PyroFlex™ Thermal Straps with HCCF Fittings in shipping fixture. |
![]() Pictured: 2 Flight Model PyroFlex™ Thermal Straps with HCCF Fittings and posts for Sensors. |
WHICH CARBON-BASED STRAP IS BEST FOR YOUR APPLICATION?
TAI offers multiple carbon-based strap products because no single configuration or material is ideal under all operational and environmental conditions. Pictured (left to right): GraFlex I, GraFlex II, Graphene Foils, and Pyrolytic Graphite Film Straps from TAI.
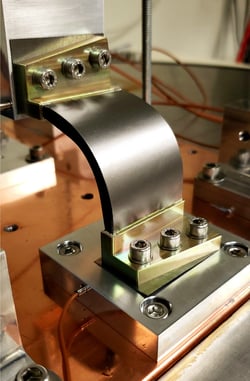
LAYERED GRAPHENE FOIL (LGF) AND MICRO-CRACKING
While TAI has extensive experience designing and testing our layered graphene foil-based straps (and our PyroFlex™ & GTL™ products have been tested by NIST researchers), our team will only offer a graphene layered foil solution under extremely limited applications and operating environments, due to issues with commercially-available layered graphene foil thermal links.
As our customers and colleagues at NASA, NIST, the Indian Space Research Organization (ISRO), and the European Space Agency (ESA) have all noted and experienced firsthand (either with graphene foil thermal links/straps, or individual graphene foil sheets), one critical problem plagues all layered graphene foils and composite sheets: "micro-cracking" or stress fractures. These tiny cracks are caused by flexing/bending the strap assemblies (or sheets), and even occur with the minimal movements associated with minute levels of thermal expansion and contraction. These fractures can grow over time (in just a matter of a few cycles), and eventually lead to reduced performance, damaged foils, and compromised straps.
Additionally, tests performed by NIST researchers demonstrated that layered graphene foil-based thermal links experienced significant performance degradation after being thermally-cycled (just two additional cycles can result in conductance losses of >15% at 160K). As a result, TAI will not provide layered graphene foil thermal links to any application operating under 200K, and any application with a wide range of motion/deflection requirements.